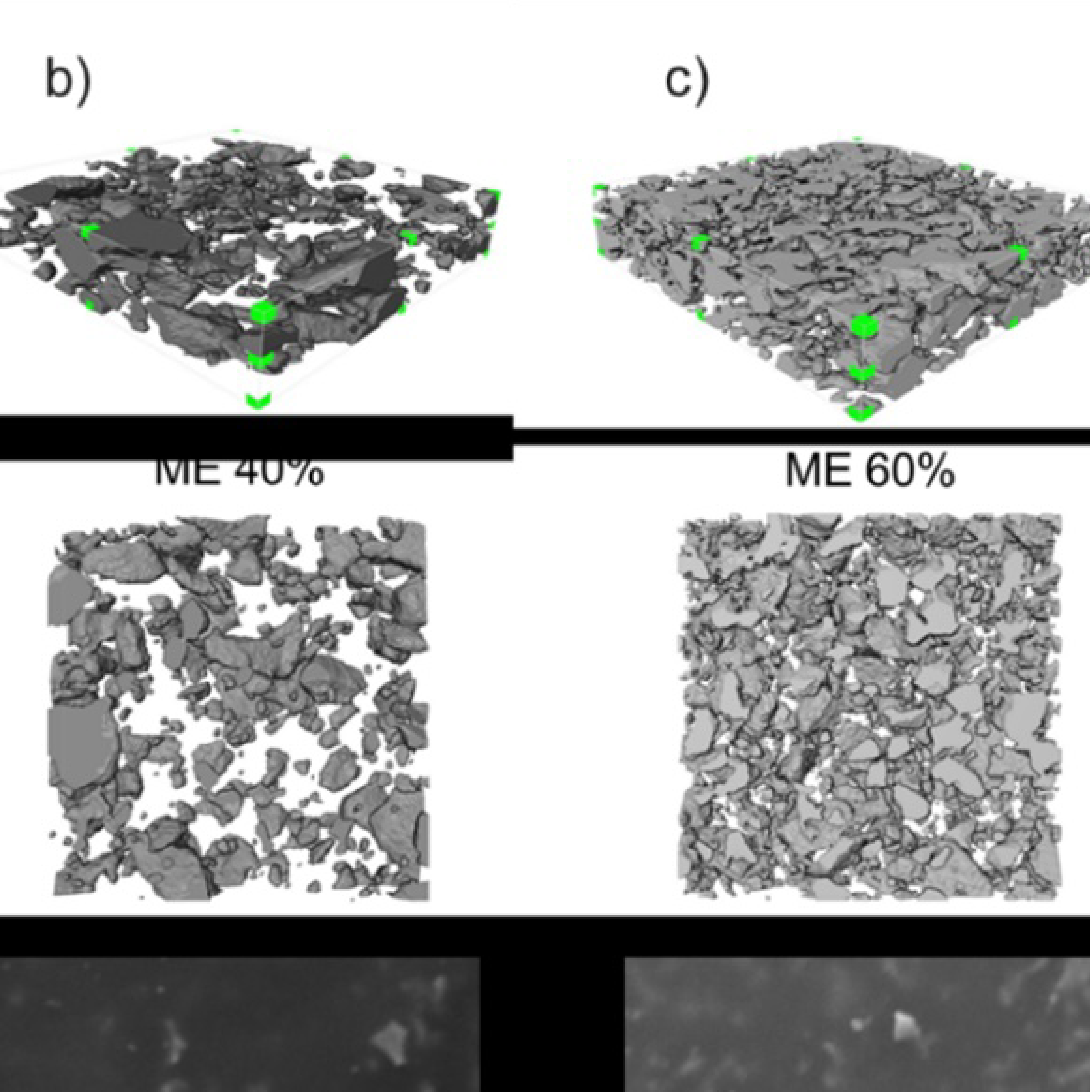
3D Microstructure of Soft Magnetic Elastomer Membrane
Soft magnetic elastomer membranes enable fast magnetic actuation under low fields. In our project, we… Read More
Events & Resources
News, Events and Resources from NXCT Partners
Background
Natural materials can feature exceptionally well-ordered and complex composite microstructures that may out-perform the sum of their individual components. For example, mollusc shells contain a thin layer of nacre (mother-of-pearl), which is much better at absorbing damage compared to Aragonite, the calcium carbonate mineral that it is predominantly made of. This is due to extrinsic toughening mechanisms, like crack deflection, bridging and material pull-out that are generated at the nano-, micro-, and millimetre scale. However, manufacturing bio-inspired, high-performance composites with constituents presenting intricate and defect-free microstructures arranged on various length scales is a difficult challenge. One key issue revolves around the visualisation complex, small-scale architectures of fabricated materials.
Project details and results
Figure 1 shows a cylindrical object (35 x 30 mm diameter) that was fabricated via the controlled freeze-driven solidification in one direction (z-axis) of a suspension of particles (“unidirectional freeze-casting”). μ-CT -based analysis shows over 90 % porosity, with pores that are roughly 40 μm in diameter and macroscopically aligned along one plane. However, the alignment of freeze-cast material is not entirely uniform: (1) the prototype mould used caused the development of a fan-like appearance of ceramic lamellae across the length (y-axis), and (2) a large temperature gradient in proximity to the freezing interface generated a dense area of material through the first millimetre of the component (Figure 2).
How has X-ray CT benefited your research?
The involvement of μ-CT imaging equipment at NXCT has been a powerful, non-destructive, multi-scale 3D analysis tool in this work.
Future impact
Further fabrication strategies will include infiltrating freeze-cast bodies with dilute suspensions of graphene oxide (GO) to generate vast layering between the two components. Spark Plasma Sintering will consolidate ceramic-GO pre-forms into dense ceramic-rGO materials with alignment of the graphene-like reinforcement. Ultimately, this aims to improve the fracture characteristics of ceramic-based materials with a small amount (<1 wt.%) of structurally ordered, graphene filler.
“The imaging analysis that has taken place demonstrates an ability to visualise micron-scale architecture in a non-destructive manner, reducing the number of sacrificial bodies used during characterisation. This becomes important when a small batch of specimens is made, commonly seen within lab scale production.”
Joseph Alemzadeh, PhD Research Student at Cardiff University
Figure 1: Photograph and 3D reconstructions of an alumina scaffold generated via freeze-casting. The z-axis refers to the direction of freezing during the casting process. Scan resolution = 4.52 μm, retrieved with a 225kVp Nikon/X-tek HMX μ-CT scanner (Nikon Metrology, UK).
Figure 2: Left) 3D reconstruction of the core region of the alumina scaffold. Scan resolution = 4.52 μm, retrieved with a 225 kVp Nikon/X-tek HMX μ-CT scanner (Nikon Metrology, UK). Right) High-resolution, cross-sectional image illustrating the dense, solid region that features in freeze-cast materials. Scan resolution = 688 nm, retrieved with a 160 kVp Zeiss Xradia Versa 510 X-ray microscope μ-CT scanner (Carl Zeiss, Germany).
Soft magnetic elastomer membranes enable fast magnetic actuation under low fields. In our project, we… Read More
Nowadays, the increasing capability of micro-manufacturing processes enables the manufacture of miniature products with extremely… Read More
Injection of CO2 into shale reservoirs to enhance gas recovery and simultaneously sequester greenhouse… Read More