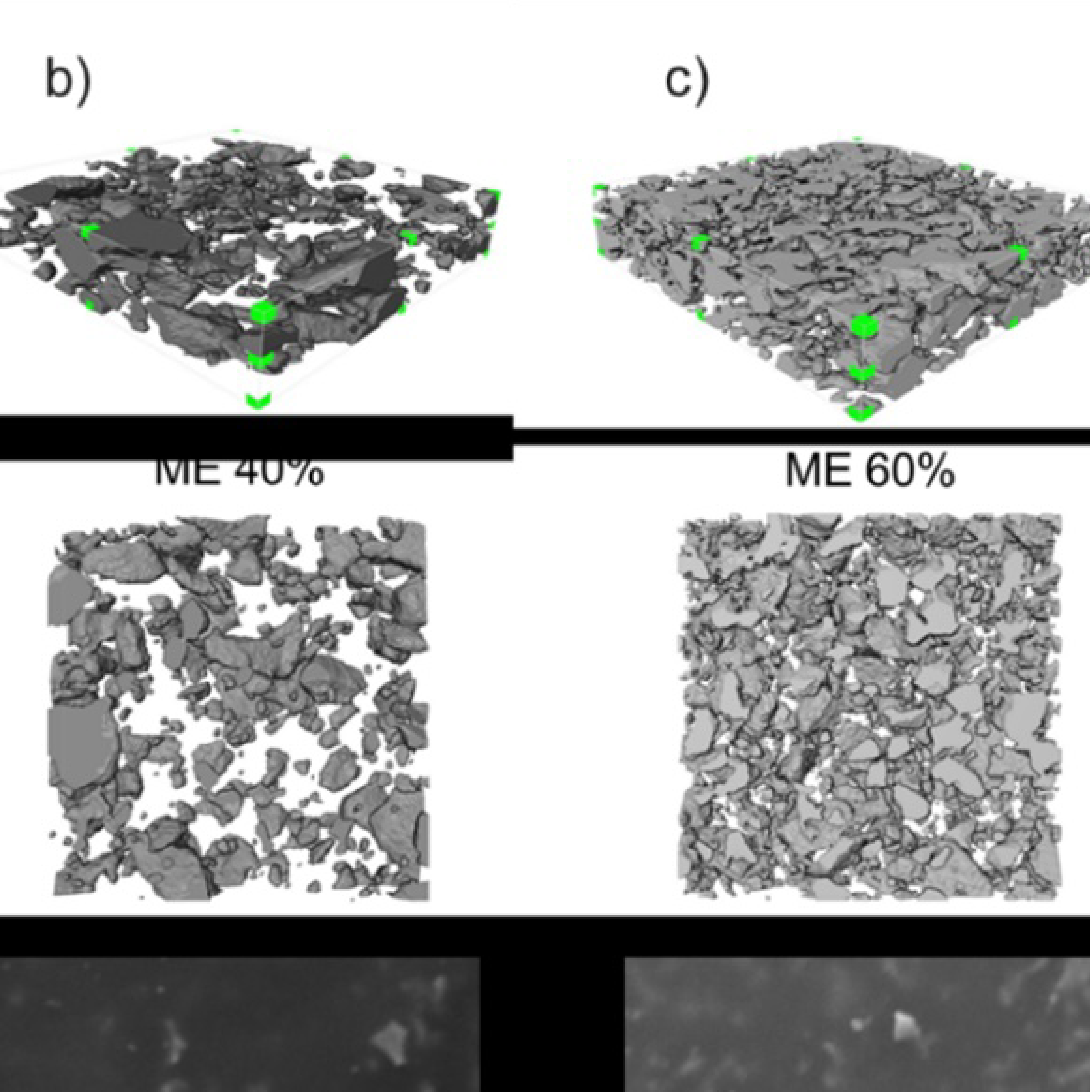
3D Microstructure of Soft Magnetic Elastomer Membrane
Soft magnetic elastomer membranes enable fast magnetic actuation under low fields. In our project, we… Read More
Events & Resources
News, Events and Resources from NXCT Partners
3D printing is innovating many industrial sectors and has the potential to enhance also the manufacture of biologics. We developed a new material formulation to 3D print perfectly ordered purification devices. This project employs micro-computed tomography to reconstruct the internal morphology of 3D printed perfectly ordered structures enhancing our understanding of 3D printing process.
Bioseparations and purifications often relies on packed porous spheres randomly arranged within a cylindrical vessel. This technology is characterised by high surface area available for cell adhesion, adsorption and mass transfer, although it suffers the negative effects of fluid dispersion, column-to-column variability, poor predictability.
3D printing enables the fabrication of perfectly ordered morphologies with good reproducibility, at high speed (1 litre columns could be printed overnight) and relatively low cost. Until now, its application in bioprocessing has been hindered due to the lack materials that are biocompatible and can be 3D printed at high resolution (finest features currently around 300 µm for bioseparation applications).
Our group has focused on the development of novel polymeric formulations with adjusted chemical and porous properties that can be 3D printed using Digital light processing (DLP) technique. The formulation consists of bifunctional monomers that polymerise upon light exposure creating the polymeric network.
To ensure the formation of pores at nanoscale, we introduce into the material formulation pore forming agents such as organic solvents that remain unchanged during the polymerisation and are washed away once the object is printed.
Our results show that it is possible to 3D print structures of highly complex geometries (e.g. Schoen gyroid with up to 200 µm channels) and pore size from 10 nm to 1000 nm. However, due to the complicate chemistry involved in the printing process, unwanted phenomena such as light scattering and overcuring can be detrimental for the manufacture of homogeneous structures.
Micro-computed tomography is a very useful tool to fully determine the internal morphology of 3D printed columns both at micro and nanometre scale. Our aim is to employ micro-computed tomography to compare printed perfectly ordered columns against the originally designed CAD file. In addition, we want to ensure that all printed channels are unblocked and remained unaffected during the photopolymerisation.
This project will enhance our understanding of the printing process enabling fully exploitation of perfectly ordered purification devices to fit current bioprocessing challenges.
We use 3D printing to fabricate complex geometries such as Schoen gyroid with a designed external porosity at the microscale level and an inherent porosity at the nanoscale level. This process combines 3D printing via photopolymerisation and phase-induced separation.
Micro computed tomography (µCT) can be used to obtain detailed reconstruction of 3D structures. Porosity, pore diameter, tortuosity and spatial homogeneity could be revealed using µCT and compared against CAD model. This will ultimately enhance the understanding of 3D printing process, internal morphology and structure homogeneity.Mariachiara Conti, PhD researcher, The University of Edinburgh
Dr. Thomas Johnson
Dr. Francesco Iacoviello
Dr. Simone Dimartino
CAD rendering of a Schoen gyroid with 300 µm channels with a designed external porosity of 50% and wall thickness of 300 µm.
Soft magnetic elastomer membranes enable fast magnetic actuation under low fields. In our project, we… Read More
Nowadays, the increasing capability of micro-manufacturing processes enables the manufacture of miniature products with extremely… Read More
Injection of CO2 into shale reservoirs to enhance gas recovery and simultaneously sequester greenhouse… Read More