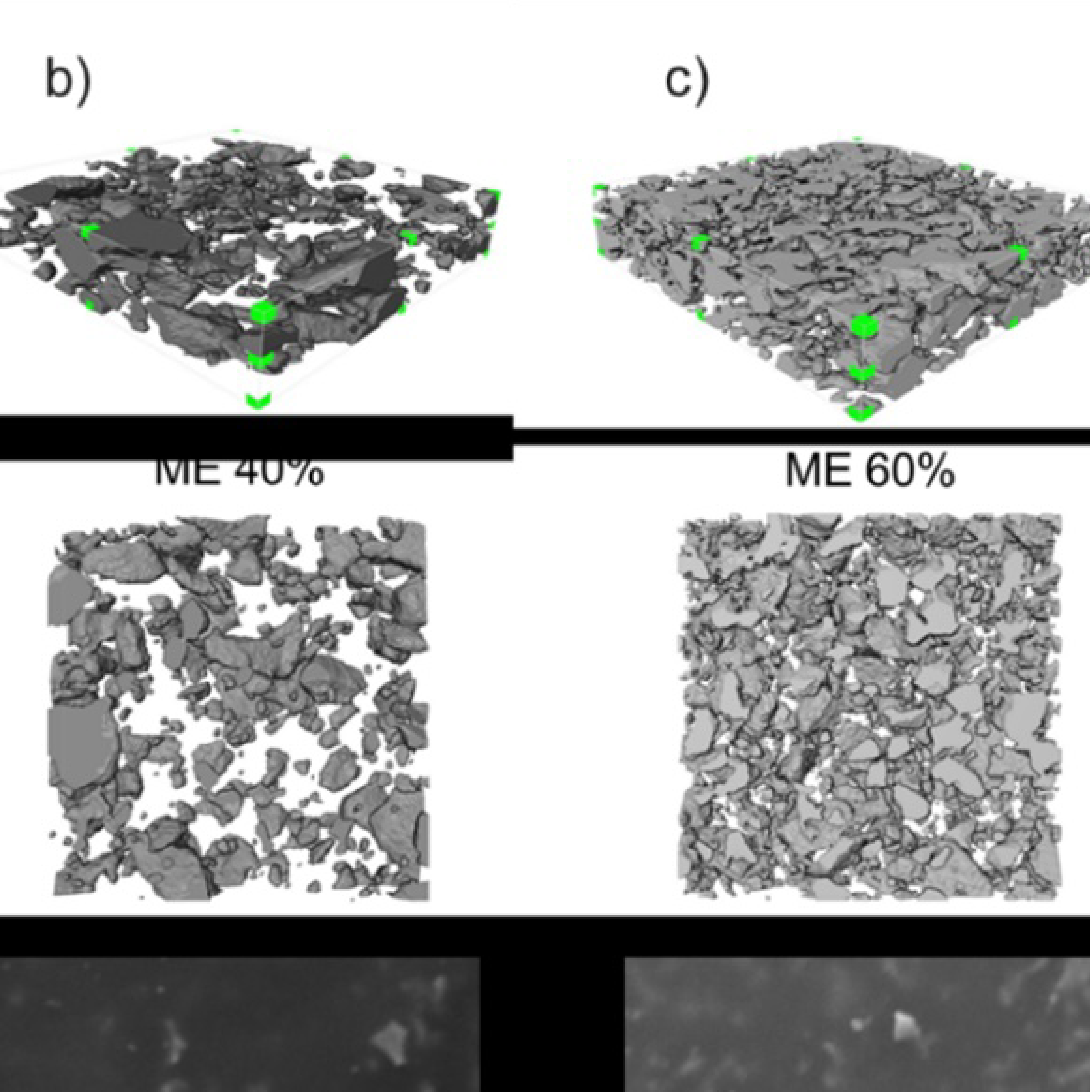
3D Microstructure of Soft Magnetic Elastomer Membrane
Soft magnetic elastomer membranes enable fast magnetic actuation under low fields. In our project, we… Read More
Events & Resources
News, Events and Resources from NXCT Partners
The high temperature materials research group at the University of Oxford is working to understand cracking during additive manufacturing. The aim of our collaboration with NXCT was to characterize the 3D nature of micro-cracks and the presence of porosity in engineering components produced from different alloys.
Conventional high gamma prime nickel-based superalloys crack during laser-powder bed fusion additive manufacturing. In order to 3D-print reliable and high quality engineering components free of defects the factors that bring about these cracks are studied. Conventional metallurgical techniques such as scanning electron microscopy can help elucidate specific crack mechanisms but are not suitable for characterizing the 3D nature and path that the cracks follow.
Collaboration with NXCT has resulted in an understanding of how build direction influences crack propagation as well as the influence of geometry on the degree of porosity and cracking that takes place during 3D printing. This can be used to develop crack resistant alloys, optimize processing conditions, and tailor the engineering component for improved quality.
Fig: Slices of the CM247LC blade sample as observed by XCT and 3D reconstruction of cracks as observed on two different planes.
A New Class of Alumina-Forming Superalloy for 3D Printing accepted for publication in Additive Manufacturing (2022)
”With the support of NXCT we were able to characterize the nature of micro-cracking and porosity in 3D-printed Ni-based superalloy components. The density of these alloys and the length scale of the defects made characterization of these features challenging and highly novel. The results produced –published in Additive Manufacturing – would not be possible without the collaboration with NXCT.”
Dr Joseph Ghoussoub, University of Oxford
Soft magnetic elastomer membranes enable fast magnetic actuation under low fields. In our project, we… Read More
Nowadays, the increasing capability of micro-manufacturing processes enables the manufacture of miniature products with extremely… Read More
Injection of CO2 into shale reservoirs to enhance gas recovery and simultaneously sequester greenhouse… Read More